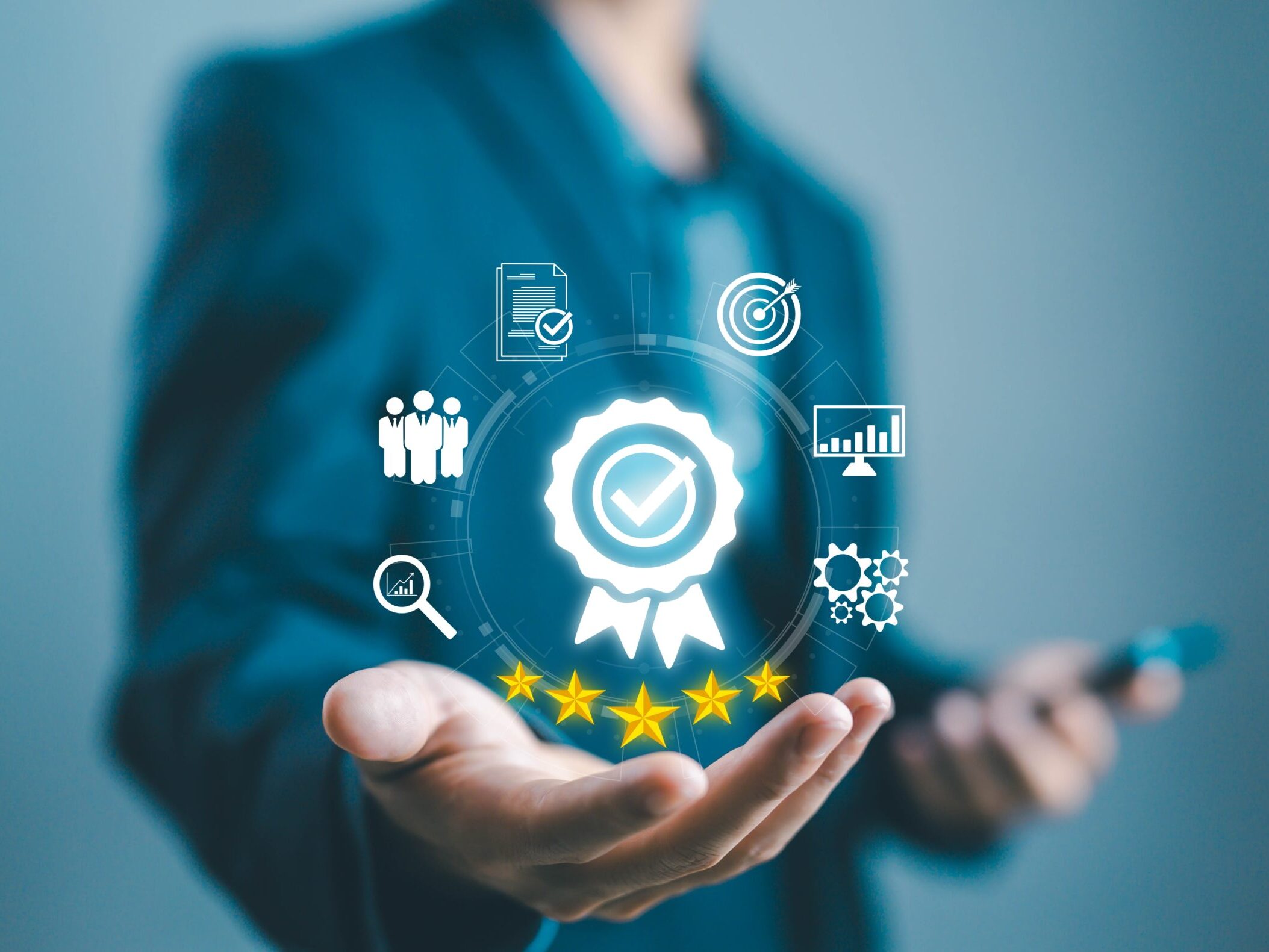
Product Quality Control (QC)
Our integrated QC and QA programs are crucial in ensuring that products meet specified requirements and customer expectations. These programs help maintain product consistency, reduce defects, and ensure compliance with industry regulations, preserving our high level of customer satisfaction.
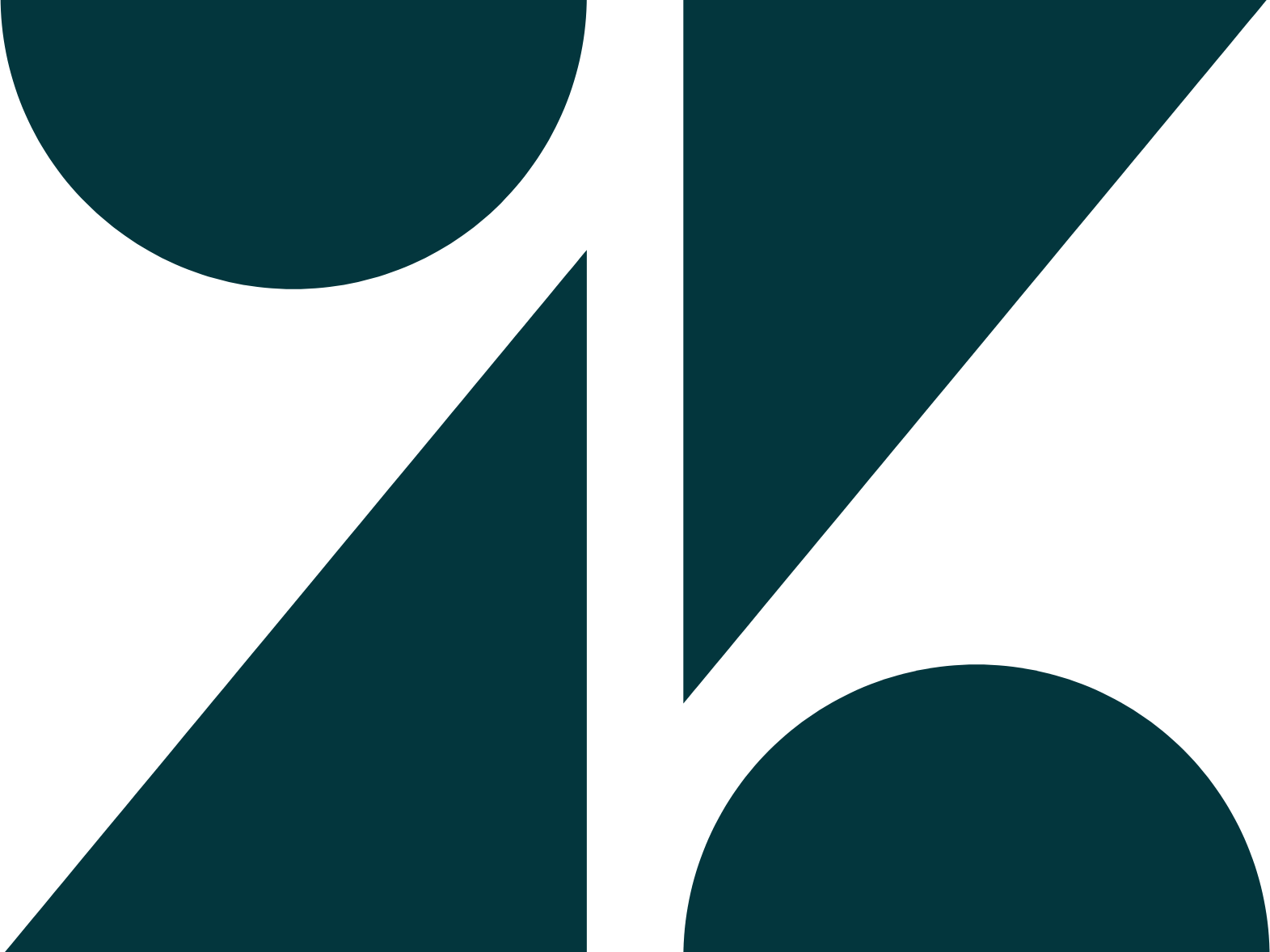
Zendesk – Customer Complaint Management
If, on the rare occasion an error occurs we use Zendesk to manage the process and resolve these concerns quickly and effectively. Zendesk is our ticketing system used to manage customer interactions and resolve concerns or questions. It facilitates seamless information flow, assigns responsibility, and tracks progress throughout the ticket’s lifecycle. This enables us to monitor performance, measure results, and identify trends for continuous improvement.
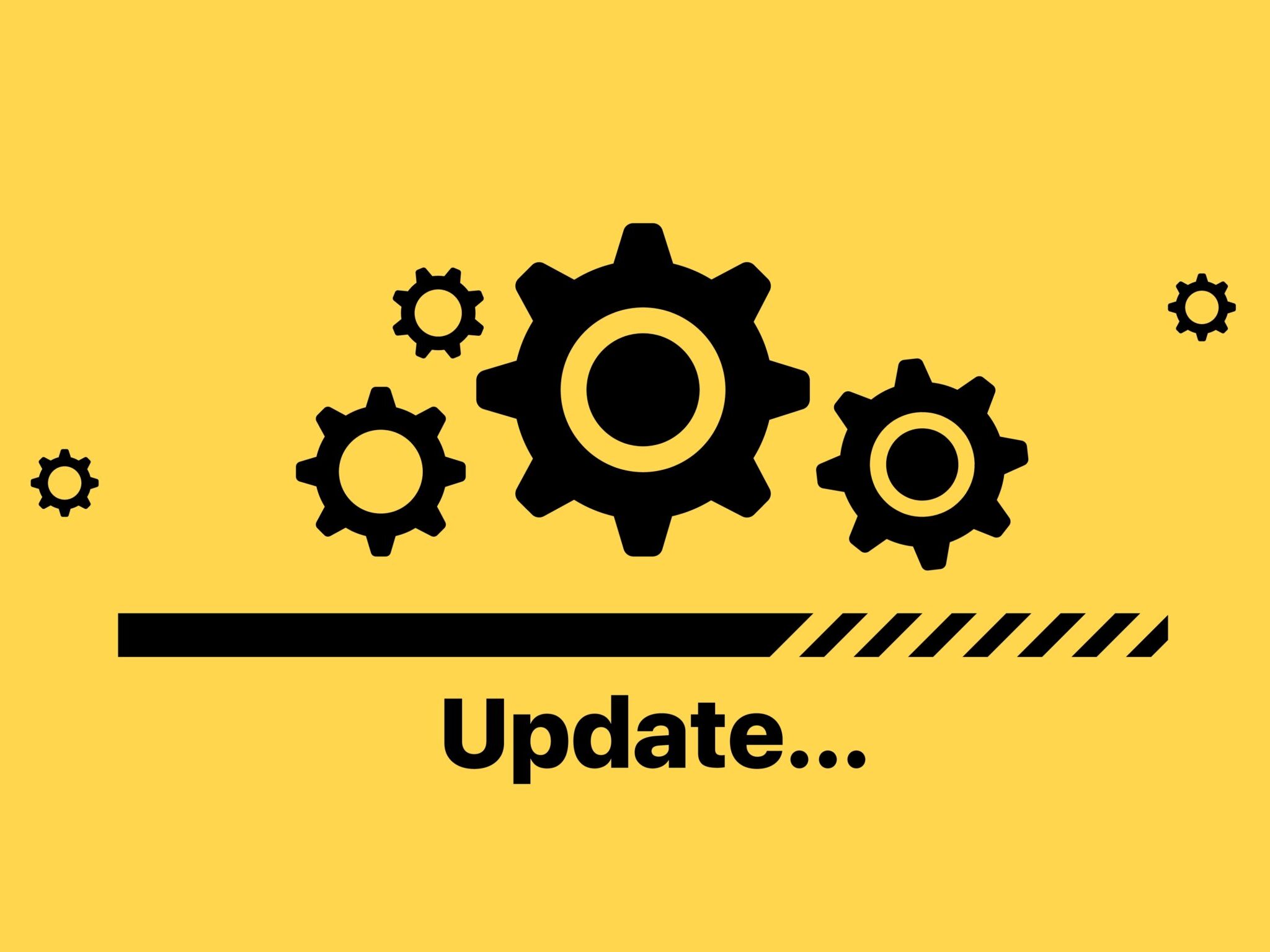
New Product Development (NPD) QA
Our NPD QA is essential in developing and validating product designs and ensuring compliance. Our team provides reassurance that newly developed products meet the initial requirements before progressing to the manufacturing stage. Embedded within our design and project teams, NPD QA adds value, skills, and expertise to enhance project success and meet customer expectations. The quality tools employed to enhance this process include:
– APQP – Advanced Product Quality Planning
– PPAP – Production Part Approval Process (QC)
– DFMEA – Design Failure Mode and Effects Analysis
– PFMEA – Process Failure Mode and Effects Analysis
– DVPR – Design Verification Plan & Report